2025 Autora: Howard Calhoun | [email protected]. Última modificació: 2025-01-24 13:13
El mineral de ferro s'obté de la manera habitual: mineria a cel obert o subterrània i posterior transport per a la preparació inicial, on el material és triturat, rentat i processat.
El mineral s'aboca a un alt forn i s'aboca amb aire calent i calor, que el converteix en ferro fos. Després s'elimina del fons del forn en motlles coneguts com a porcs, on es refreda per produir ferro brut. Es converteix en ferro forjat o es transforma en acer de diverses maneres.
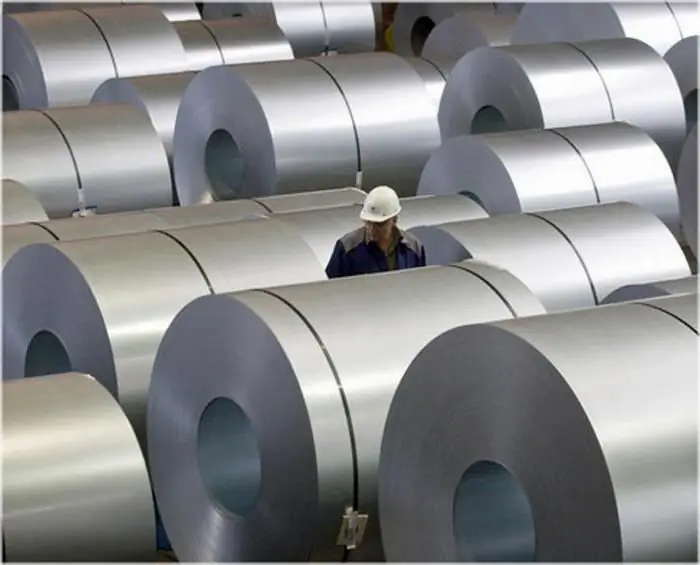
Què és l'acer?
Al principi hi havia ferro. És un dels metalls més comuns a l'escorça terrestre. Es pot trobar gairebé a tot arreu, en combinació amb molts altres elements, en forma de mineral. A Europa, el treball del ferro es remunta al 1700 aC
L'any 1786, els científics francesos Berthollet, Monge i Vandermonde van determinar amb precisió que la diferència entre ferro, ferro colat i acer es deu al contingut de carboni diferent. No obstant això, l'acer, fet de ferro, es va convertir ràpidament en el metall més important de la Revolució Industrial. A principis del segle XX, la producció mundial d'acer era de 28milions de tones - això és sis vegades més que el 1880. A l'inici de la Primera Guerra Mundial, la seva producció era de 85 milions de tones. Durant diverses dècades, pràcticament ha substituït el ferro.
El contingut de carboni afecta les característiques del metall. Hi ha dos tipus principals d'acer: aliat i no aliat. L'aliatge d'acer es refereix a elements químics diferents del carboni afegit al ferro. Així, s'utilitza un aliatge d'un 17% de crom i un 8% de níquel per crear acer inoxidable.
Actualment, hi ha més de 3000 marques catalogades (composicions químiques), sense comptar les creades per cobrir necessitats individuals. Tots ells contribueixen a fer de l'acer el material més adequat per als reptes del futur.
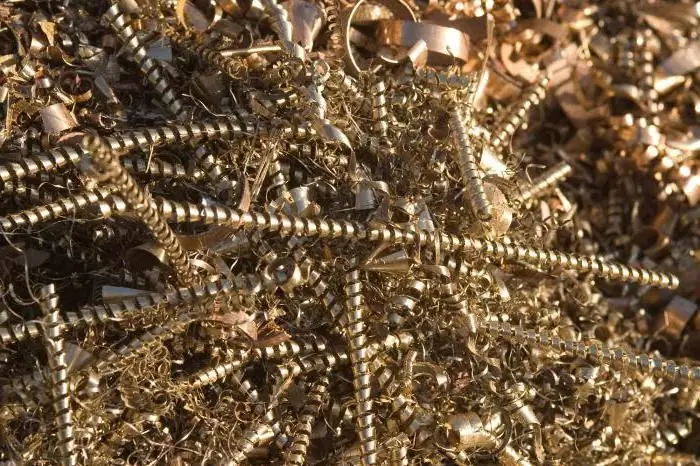
Matèries primeres siderúrgiques: primàries i secundàries
La fusió d'aquest metall amb molts components és el mètode d'extracció més comú. Els materials de càrrega poden ser tant primaris com secundaris. La composició principal de la càrrega, per regla general, és el 55% de ferro brut i el 45% de la ferralla restant. Els ferroaliatges, el ferro colat convertit i els metalls comercialment purs s'utilitzen com a element principal de l'aliatge; per regla general, tots els tipus de metalls ferrosos es classifiquen com a secundaris.
El mineral de ferro és la matèria primera més important i bàsica de la indústria siderúrgica. Es necessiten unes 1,5 tones d'aquest material per produir una tona de ferro brut. S'utilitzen unes 450 tones de coc per produir una tona de ferro brut. Moltes ferreriesfins i tot s'utilitza carbó vegetal.
L'aigua és una matèria primera important per a la indústria siderúrgica. S'utilitza principalment per a l'extinció del coc, la refrigeració d' alts forns, la producció de vapor de la porta del forn de carbó, el funcionament d'equips hidràulics i l'eliminació d'aigües residuals. Es necessiten unes 4 tones d'aire per produir una tona d'acer. El flux s'utilitza a l' alt forn per extreure contaminants del mineral de la fosa. La pedra calcària i la dolomita es combinen amb les impureses extretes per formar escòries.
Tant els alts forns com els d'acer revestits amb refractaris. S'utilitzen per revestir forns destinats a la fosa de mineral de ferro. Per a l'emmotllament s'utilitza diòxid de silici o sorra. Els metalls no fèrrics s'utilitzen per produir acer de diferents graus: alumini, crom, cob alt, coure, plom, manganès, molibdè, níquel, estany, tungstè, zinc, vanadi, etc. Entre tots aquests ferroaliatges, el manganès és molt utilitzat en la fabricació d'acer..
Els residus de ferro d'estructures de fàbriques desmantellades, maquinària, vehicles antics, etc. es reciclen i s'utilitzen àmpliament a la indústria.
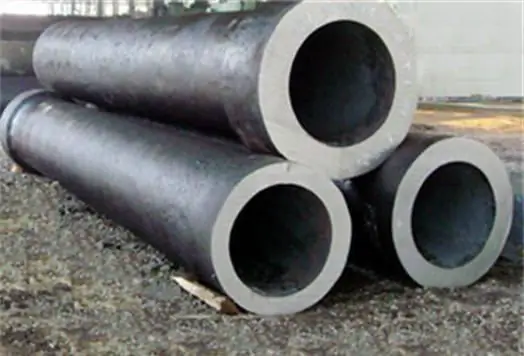
Ferro per acer
La fosa d'acer amb ferro colat és molt més habitual que amb altres materials. El ferro colat és un terme que sol referir-se al ferro gris, però també s'identifica amb un gran grup de ferroaliatges. El carboni representa entre un 2,1 i un 4% en pes, mentre que el silici és normalment entre un 1 i un 3% en pes a l'aliatge.
La fosa de ferro i acer té lloc a una temperaturapunt de fusió entre 1150 i 1200 graus, que és uns 300 graus més baix que el punt de fusió del ferro pur. El ferro colat també presenta una bona fluïdesa, una excel·lent mecanització, resistència a la deformació, l'oxidació i la fosa.
L'acer també és un aliatge de ferro amb un contingut de carboni variable. El contingut de carboni de l'acer és del 0,2 al 2,1% en massa, i és el material d'aliatge més econòmic per al ferro. La fosa d'acer a partir de ferro colat és útil per a diversos propòsits d'enginyeria i estructurals.
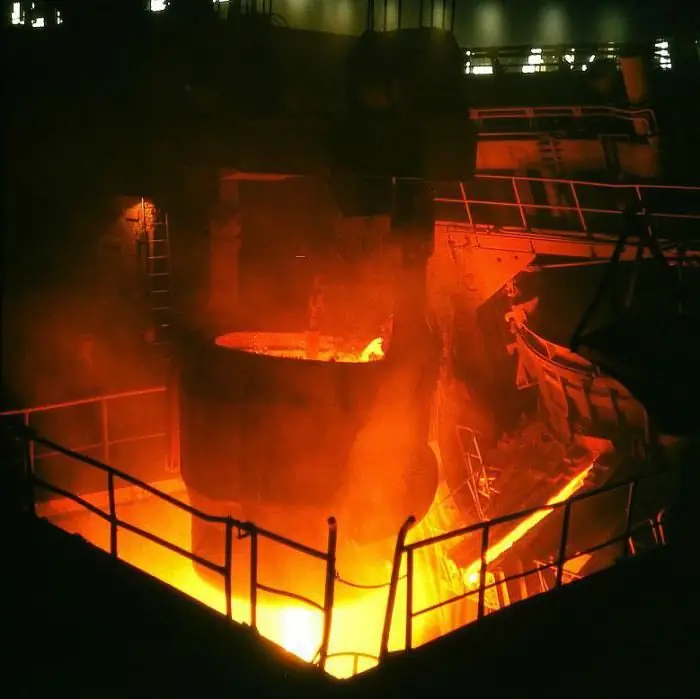
Mineral de ferro per a acer
El procés d'elaboració d'acer comença amb el processament del mineral de ferro. La roca que conté mineral de ferro es tritura. El mineral s'extreu amb corrons magnètics. El mineral de ferro de gra fi es processa en grumolls de gra gruixut per utilitzar-los en un alt forn. El carbó es refina en un forn de coc per produir una forma gairebé pura de carboni. A continuació, la barreja de mineral de ferro i carbó s'escalfa per produir ferro fos, o ferro brut, del qual es fa acer.
Al forn principal d'oxigen, el mineral de ferro fos és la matèria primera principal i es barreja amb diverses quantitats d'acer de ferralla i aliatges per produir diferents graus d'acer. En un forn d'arc elèctric, la ferralla d'acer reciclat es fon directament en acer nou. Al voltant del 12% de l'acer està fet de material reciclat.
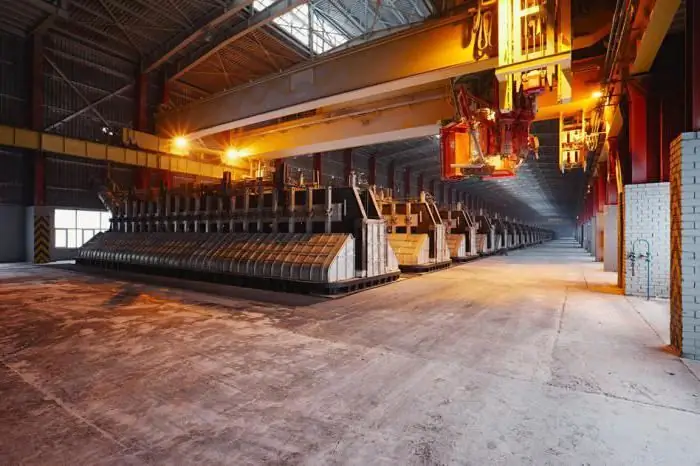
Tecnologia de fosa
La fosa és un procés pel qual s'obté un metall en forma d'element,ja sigui com a compost simple del seu mineral escalfant-se per sobre del seu punt de fusió, generalment en presència d'agents oxidants com l'aire o agents reductors com el coc.
A la tecnologia de fabricació d'acer, el metall que es combina amb l'oxigen, com l'òxid de ferro, s'escalfa a una temperatura elevada i l'òxid es forma en combinació amb el carboni del combustible, que s'allibera com a monòxid de carboni o carboni. diòxid. Les altres impureses, anomenades col·lectivament venes, s'eliminen afegint-hi un corrent amb el qual es combinen per formar escòries.
La fabricació d'acer moderna utilitza un forn de reverberació. El mineral i el corrent concentrats (generalment pedra calcària) es carreguen a la part superior, mentre que el mat fos (compost de coure, ferro, sofre i escòries) s'extreu de la part inferior. És necessari un segon tractament tèrmic en un forn convertidor per eliminar el ferro de l'acabat mat.
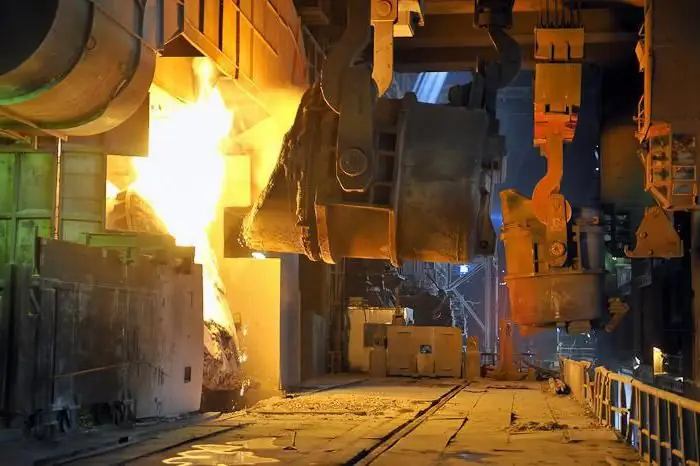
Mètode del convector d'oxigen
El procés BOF és el procés de fabricació d'acer líder del món. La producció mundial d'acer convertidor l'any 2003 va ascendir a 964,8 milions de tones o el 63,3% de la producció total. La producció de convertidors és una font de contaminació ambiental. Els principals problemes d'aquesta són la reducció d'emissions, abocaments i reducció de residus. La seva essència rau en l'ús d'energia secundària i recursos materials.
La calor exotèrmica es genera per reaccions d'oxidació durant la ventilació.
El procés principal de fabricació d'acer utilitzant el nostreexistències:
- El ferro fos (de vegades anomenat metall calent) d'un alt forn s'aboca en un gran recipient revestit refractari anomenat cullera.
- El metall de la cullera s'envia directament a l'etapa principal de producció d'acer o de pretractament.
- S'injecta oxigen d' alta puresa a una pressió de 700-1000 quilopascals a velocitat supersònica a la superfície del bany de ferro a través d'una llança refrigerada per aigua que es suspèn en un recipient i es manté uns peus per sobre del bany.
La decisió del pretractament depèn de la qualitat del metall calent i de la qualitat d'acer final desitjada. Els primers convertidors inferiors extraïbles que es poden desenganxar i reparar encara estan en ús. S'han canviat les llances utilitzades per bufar. Per evitar l'encallament de la llança durant el bufat, es van utilitzar collars ranurats amb una llarga punta de coure afilada. Les puntes de la punta, després de la combustió, cremen el CO format quan s'infla en CO2 i proporcionen calor addicional. Per eliminar l'escòria s'utilitzen dards, boles refractàries i detectors d'escòries.
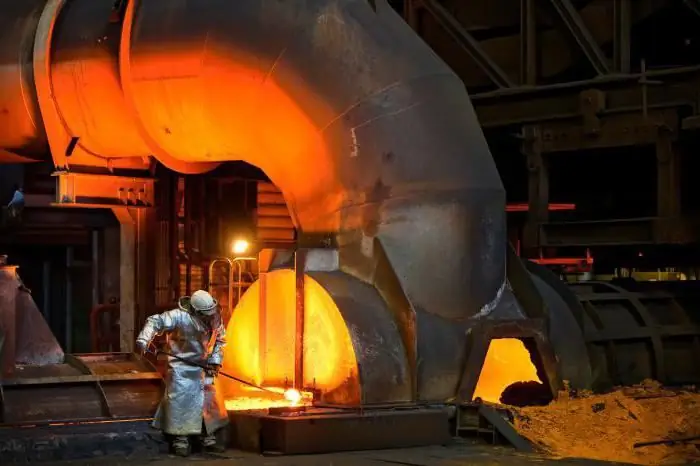
Mètode convector d'oxigen: avantatges i desavantatges
No requereix el cost dels equips de purificació de gasos, ja que la formació de pols, és a dir, l'evaporació del ferro, es redueix 3 vegades. A causa de la disminució del rendiment del ferro, s'observa un augment del rendiment d'acer líquid entre un 1,5 i un 2,5%. L'avantatge és que la intensitat del bufat en aquest mètode augmenta, la qual cosa dónala capacitat d'augmentar el rendiment del convertidor en un 18%. La qualitat de l'acer és més alta perquè la temperatura a la zona de purga és més baixa, la qual cosa provoca una menor formació de nitrogen.
Les deficiències d'aquest mètode de fosa d'acer van provocar una disminució de la demanda de consum, ja que el nivell de consum d'oxigen augmenta un 7% a causa de l'elevat consum de combustió de combustible. Hi ha un augment del contingut d'hidrogen en el metall reciclat, per això es necessita un temps després del final del procés per dur a terme una purga amb oxigen. Entre tots els mètodes, el convertidor d'oxigen té la formació d'escòria més alta, la raó és la incapacitat de controlar el procés d'oxidació dins de l'equip.
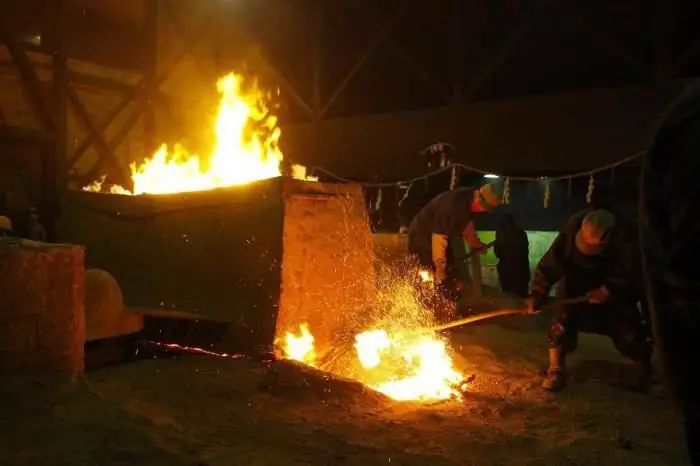
Mètode de foc obert
El procés de foc obert durant la major part del segle XX va ser la part principal del processament de tot l'acer fabricat al món. William Siemens, a la dècada de 1860, va buscar un mitjà per augmentar la temperatura en un forn metal·lúrgic, ressuscitant una vella proposta d'utilitzar la calor residual generada pel forn. Va escalfar el maó a una temperatura elevada i després va utilitzar el mateix camí per introduir aire al forn. L'aire preescalfat va augmentar significativament la temperatura de la flama.
El gas natural o els olis pesats atomitzats s'utilitzen com a combustible; l'aire i el combustible s'escalfen abans de la combustió. El forn està carregat de ferro brut líquid i ferralla d'acer juntament amb mineral de ferro, pedra calcària, dolomita i fluxos.
L'estufa està fetamaterials altament refractaris com ara maons de llar de magnesita. Els forns de sol obert pesen fins a 600 tones i solen instal·lar-se en grups, de manera que els equips auxiliars massius necessaris per carregar els forns i processar l'acer líquid es poden utilitzar amb eficàcia.
Tot i que el procés de foc obert ha estat gairebé completament substituït a la majoria dels països industrialitzats pel procés bàsic d'oxigen i el forn d'arc elèctric, fa aproximadament 1/6 de tot l'acer produït a tot el món.
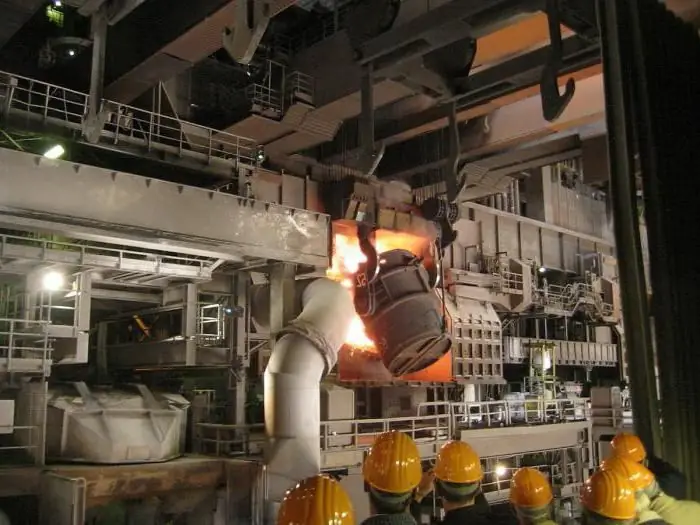
Avantatges i desavantatges d'aquest mètode
Els avantatges inclouen la facilitat d'ús i la facilitat de producció d'acer aliat amb diversos additius que donen al material diverses propietats especialitzades. Els additius i aliatges necessaris s'afegeixen immediatament abans del final de la fosa.
Els desavantatges inclouen una eficiència reduïda en comparació amb el mètode del convertidor d'oxigen. A més, la qualitat de l'acer és inferior en comparació amb altres mètodes de fosa de metalls.
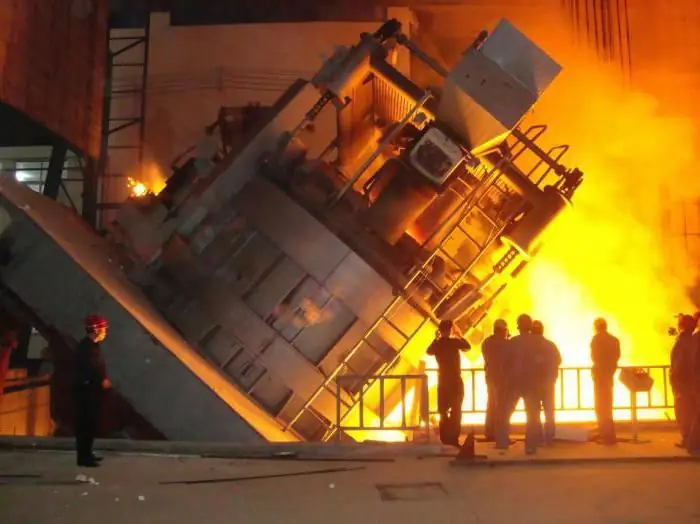
Mètode de fabricació d'acer elèctric
El mètode modern de fosa d'acer utilitzant les nostres pròpies reserves és un forn que escalfa un material carregat amb un arc elèctric. Els forns d'arc industrials varien en dimensions des de petites unitats amb una capacitat d'aproximadament una tona (utilitzades a les foneries per a la producció de productes de ferro) fins a unitats de 400 tones utilitzades en la metal·lúrgia secundària.
Forns d'arc,utilitzat en laboratoris de recerca pot tenir una capacitat de només unes desenes de grams. Les temperatures dels forns d'arc elèctric industrials poden arribar als 1800 °C (3, 272 °F), mentre que les instal·lacions de laboratori poden superar els 3000 °C (5432 °F).
Els forns d'arc es diferencien dels forns d'inducció perquè el material de càrrega està directament exposat a un arc elèctric i el corrent als terminals passa a través del material carregat. El forn d'arc elèctric s'utilitza per a la producció d'acer, consisteix en un revestiment refractari, generalment refrigerat per aigua, de grans dimensions, cobert amb un sostre retràctil.
El forn es divideix principalment en tres seccions:
- Besca formada per parets laterals i bol inferior d'acer.
- La llar consta d'un refractari que treu el bol inferior.
- El sostre refractari revestit o refrigerat per aigua es pot fer com una secció de bola o un tronc de con (secció cònica).
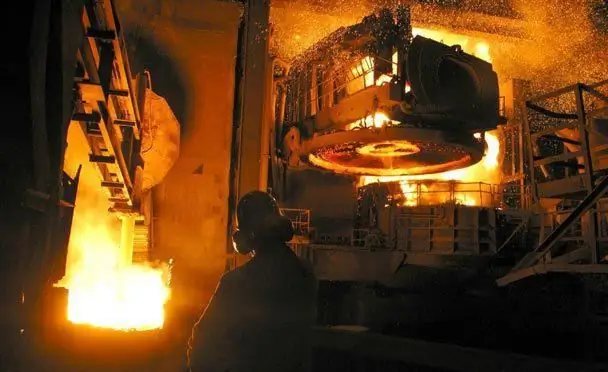
Avantatges i desavantatges del mètode
Aquest mètode ocupa una posició de lideratge en el camp de la producció d'acer. El mètode de fosa d'acer s'utilitza per crear metalls d' alta qualitat que no contenen o conté una petita quantitat d'impureses no desitjades, com ara sofre, fòsfor i oxigen.
El principal avantatge del mètode és l'ús d'electricitat per a la calefacció, de manera que podeu controlar fàcilment la temperatura de fusió i aconseguir una velocitat d'escalfament increïble del metall. El treball automatitzat es convertiràuna addició agradable a l'excel·lent oportunitat per al processament d' alta qualitat de diverses ferralla.
Els desavantatges inclouen un alt consum d'energia.
Recomanat:
Acer inoxidable alimentari: GOST. Com identificar l'acer inoxidable de qualitat alimentària? Quina diferència hi ha entre l'acer inoxidable alimentari i l'acer inoxidable tècnic?

L'article parla dels graus d'acer inoxidable de qualitat alimentària. Llegiu com distingir l'acer inoxidable alimentari dels tècnics
Acer resistent a la corrosió. Qualitats d'acer: GOST. Acer inoxidable - preu
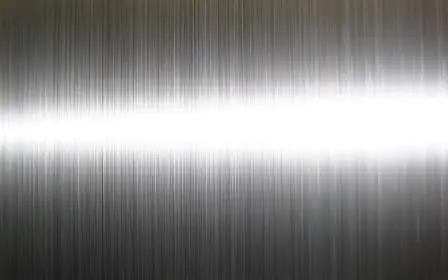
Per què es descomponen els materials metàl·lics. Què són els acers i aliatges resistents a la corrosió. Composició química i classificació segons el tipus de microestructura d'acer inoxidable. Factors que afecten els preus. Sistema de designació de grau d'acer (requisits GOST). Àrea d'aplicació
Obtenció d'alcohols: mètodes i matèries primeres
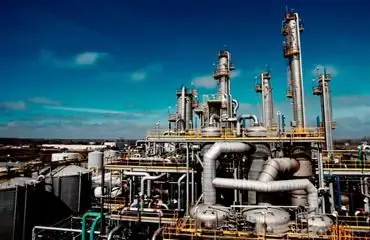
L'obtenció d'alcohols és un procés tecnològic força complicat. Hi ha mètodes bioquímics i químics per obtenir alcohols. L'obtenció d'alcohol metílic es realitza mitjançant l'ús de diverses tecnologies
Producció d'escuma de poliuretà: tecnologia, matèries primeres, equipament
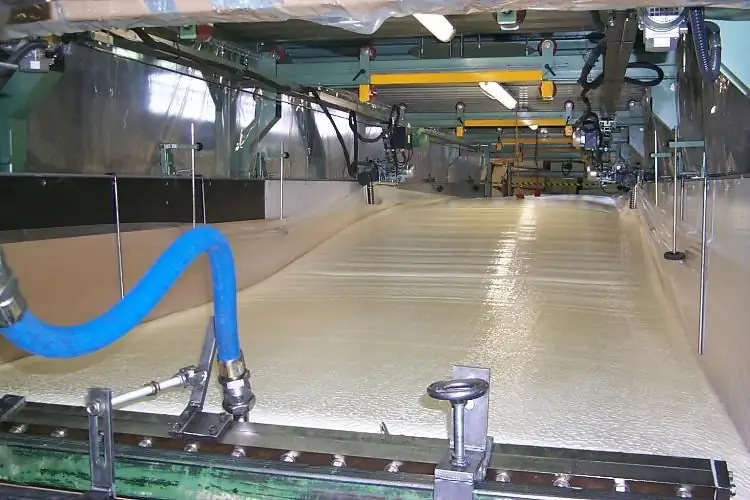
L'escuma de muntatge dels mitjans habituals de segellar les obertures de les finestres ha passat durant molt de temps a l'estat de material de construcció complet, que s'utilitza àmpliament en una varietat de tipus de treball. La varietat d'aplicacions d'aquest producte també determina la necessitat d'un enfocament diferenciat a les tecnologies de fabricació. No obstant això, les diferències en els mètodes de producció d'escuma de poliuretà són més de naturalesa cosmètica, sense afectar els processos tecnològics bàsics
Producció de canonades de PVC: tecnologia, matèries primeres i equips
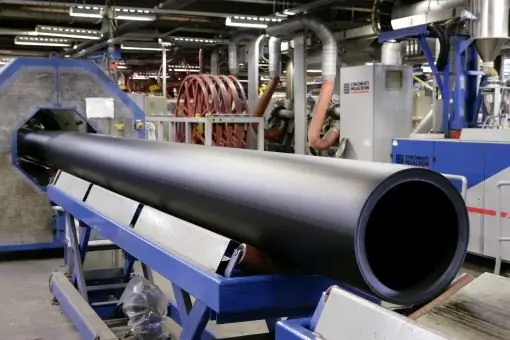
Els productes tubulars basats en clorur de polivinil (PVC) s'utilitzen àmpliament avui en dia en diverses àrees i indústries, des del sector privat fins a grans empreses de petroli i gas. Però el procés de consolidació al mercat va ser gradual, ja que les propietats físiques i tècniques del material polimèric són inferiors a les contraparts metàl·liques tradicionals en una sèrie de criteris. Tanmateix, la producció moderna de canonades de PVC, a causa de la introducció de tecnologies avançades, ha augmentat significativament el rendiment dels productes